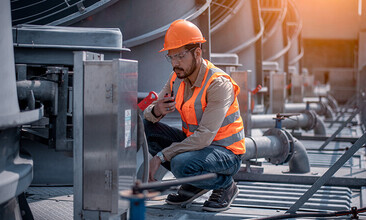
USING PREDICTIVE MAINTENANCE TO MONITOR CRITICAL PARAMETERS
Data from predictive maintenance sensors enables companies to anticipate equipment issues and take proactive measures to mitigate them.
A well-thought-out maintenance strategy is essential for safeguarding a company's assets. As traditional reactive and preventive maintenance methods become outdated, predictive maintenance is gaining traction.
This is partially due to the fact that companies have becoming increasingly comfortable with smarter technologies. They realize that they can use sophisticated analytical tools and processes to leverage the data collected from predictive maintenance sensors. This data enables them to anticipate equipment issues and take proactive measures to mitigate them.
In the past, organizations simply reacted to problems and schedule periodic maintenance service calls. However, these practices can lead to productivity losses and unnecessary equipment maintenance costs.
Now, they can use the data on equipment operating conditions obtained from predictive maintenance sensors to pinpoint potential issues and resolve them before they disrupt operations.
Benefits of Predictive Maintenance
Predictive maintenance isn't just a buzzword anymore; it's a game-changer for organizations looking to minimize downtime and extend the lifes of their systems. Deloitte's research highlights the significant benefits, showing that predictive maintenance can boost productivity by 25%, reduce breakdowns by a 70%, and reduce maintenance costs by 25%.
It's no surprise that predictive maintenance has become one of the top maintenance strategies used worldwide. Market reportsreveal a staggering growth trajectory, with the global predictive maintenance market soaring to $5.93 billion in 2023 and projected to skyrocket to $32.30 billion by 2030.
How Does It Work?
Predictive maintenance sensors are at the core of this maintenance strategy, since they collect the data required for analysis. These sensors continuously monitor conditions like temperature, vibration, pressure, and operation times.
This real-time and historical data from predictive maintenance sensors gets fed into sophisticated software programs to uncover patterns, flag potential issues, or even predict equipment failures before they occur.
This information allows organizations to foresee the future state of their assets, enabling timely interventions to prevent unplanned downtime. Ultimately, it's all about boosting productivity and ensuring equipment keeps running smoothly.
Sensaphone Systems Collect and Log Critical Data
With predictive maintenance, it is important to continuously collect and log vital data about conditions and usage patterns. Sensaphone remote monitoring systems can be connected to application-specific sensors to monitor conditions like temperature, humidity, power status, and equipment status around the clock.
These systems are capable of wirelessly integrating dozen of sensors simultaneously, providing the information needed for effective preventive maintenance strategies. For example, the Sensaphone WG30 monitoring system, which supports up to 30 wireless sensors, tracks conditions like temperature, water detection and humidity. It also serves as a data logger and records up to 67,000 samples including data, date, and time.
Similarly, the cloud-based Sentinel Pro Monitoring system can be used as a data logger, capturing input/output data from third-party Modbus sensors, transducers, and programmable logic controllers. It can securely store an unlimited record of sensor readings in the cloud for analysis by predictive maintenance software.
Sensaphone Applications
Sensaphone remote monitoring systems can support the predictive maintenance strategies of a wide array of industrial sectors.
Water/Wastewater
Remote monitoring systems can be used where pumps operate on a predictable maintenance schedule. By tracking data logs of run times, these systems can accurately forecast wear and anticipate the need for replacement or servicing. This foresight helps prevent unexpected failures and premature replacements, thus prolonging the lifecycle of pump systems.
By configuring the pump's controller to log run times, the Sensaphone system can record the length of time a pump is running.This data logging capability allows operators to identify instances where pump activity surpasses manufacturer specifications, signaling the need for maintenance.Service can be scheduled before predicted failure occurs.
HVAC
Remote monitoring systems can integrate with a variety of predictive maintenance sensors offer vital insights into equipment performance, guiding technicians on the optimal timing for maintenance. They can extract critical data on conditions such as temperature, pressure, flow rate, and vibration from various components such as fans, compressors, ducts, and pumps. This data is then transmitted to the cloud for storage and analysis. The collected data can be processed and analyzed based on defined preventive maintenance models.
Data centers
Stratus EMS remote monitoring systems provide cloud-based environmental monitoring, enabling the identification of patterns and trends in monitored conditions.
With the variety of predictive maintenance sensors available on the market, we're here to assist you in selecting the right ones. We can help configure them with our remote monitoring systems to generate tailored data for your specific maintenance strategy.
Contact our sales team who can discuss your application requirements.